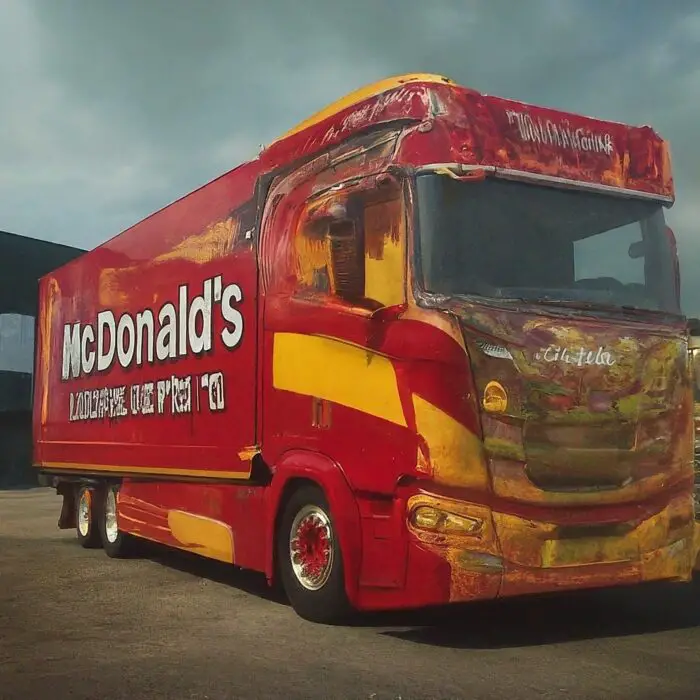
A McDonald’s delivery truck.
McDonald’s, one of the most recognizable fast-food chains in the world, serves millions of customers daily across over 100 countries.
Maintaining such a vast and consistent operation requires a highly efficient and well-organized logistics system.
This article explores how McDonald’s logistics have remained organized and intact, ensuring the seamless delivery of its products and services worldwide.
A Robust Supply Chain Network
Strategic Supplier Partnerships
McDonald’s has established long-term partnerships with reliable suppliers globally. These partnerships are built on trust, quality, and mutual growth.
By working closely with suppliers, McDonald’s ensures a steady supply of high-quality ingredients and products.
These suppliers must meet stringent quality standards, which helps maintain consistency across all McDonald’s locations.
Local Sourcing Strategy
To minimize disruptions and support local economies, McDonald’s employs a local sourcing strategy. This approach not only reduces transportation costs and environmental impact but also ensures fresher ingredients.
For instance, McDonald’s sources potatoes for its famous fries from local farmers in each region it operates. This localized sourcing is crucial for maintaining the freshness and quality of its products.
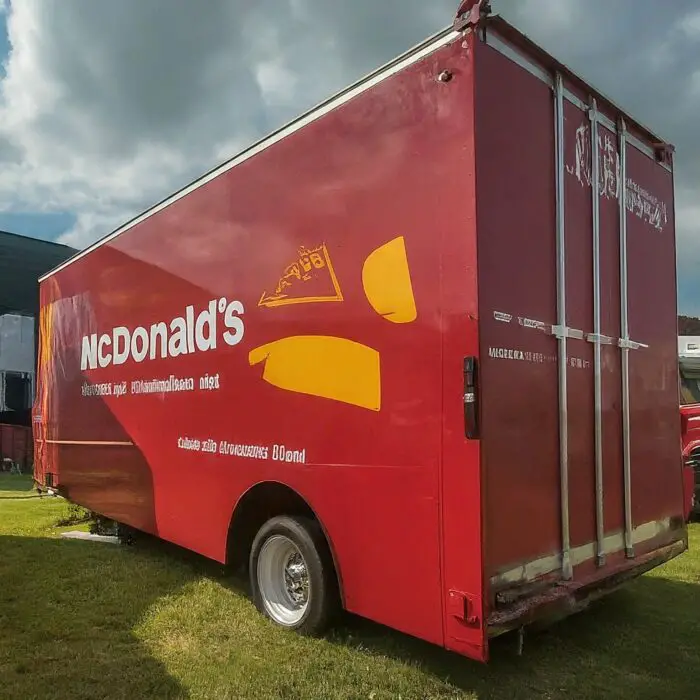
A logistics vehicle.
Efficient Distribution Centers
Hub-and-Spoke Model
McDonald’s uses a hub-and-spoke distribution model to streamline its logistics operations. Centralized distribution centers (hubs) are strategically located to serve multiple restaurants (spokes) in a specific region.
This model enhances efficiency by consolidating deliveries, reducing transportation costs, and ensuring timely replenishment of stock.
Advanced Warehousing Technologies
The use of advanced warehousing technologies is another key factor in McDonald’s logistical success. These technologies include automated inventory management systems, real-time tracking, and temperature-controlled storage facilities.
Such innovations ensure that perishable items are stored correctly and inventory levels are maintained accurately, reducing waste and ensuring product availability.
Technology Integration
Real-Time Data Analytics
McDonald’s leverages real-time data analytics to optimize its supply chain. By analyzing data from various sources, such as sales trends, weather patterns, and customer preferences, McDonald’s can make informed decisions about inventory management, demand forecasting, and supply chain adjustments.
This data-driven approach helps the company anticipate and respond to changes promptly.
Digital Order Management Systems
The integration of digital order management systems has streamlined the ordering process for McDonald’s restaurants.
These systems automate order placement, tracking, and fulfillment, reducing manual errors and improving efficiency.
Restaurants can place orders based on real-time inventory levels and sales data, ensuring they receive the right products at the right time.
Sustainability Initiatives
Sustainable Logistics Practices
McDonald’s is committed to sustainability and has implemented several initiatives to reduce its environmental footprint.
These include optimizing delivery routes to reduce fuel consumption, using energy-efficient transportation methods, and sourcing packaging materials responsibly.
By incorporating sustainability into its logistics operations, McDonald’s not only benefits the environment but also enhances its brand image.
Waste Reduction Programs
Waste reduction is a critical component of McDonald’s logistics strategy. The company has implemented comprehensive waste management programs at its distribution centers and restaurants. These programs focus on recycling, composting, and reducing food waste.
By minimizing waste, McDonald’s can lower operational costs and contribute to a more sustainable supply chain.
Crisis Management and Adaptability
Robust Contingency Plans
McDonald’s logistics system is designed to handle disruptions effectively. The company has robust contingency plans in place to address potential challenges, such as natural disasters, supply chain interruptions, and geopolitical issues.
These plans include alternative sourcing strategies, backup suppliers, and flexible distribution routes, ensuring continuity of operations even in adverse conditions.
Rapid Response Teams
In the event of a crisis, McDonald’s deploys rapid response teams to manage the situation. These teams work closely with suppliers, distribution centers, and restaurants to mitigate the impact of disruptions.
Their swift action ensures that any issues are resolved promptly, minimizing the effect on customers and operations.
Training and Development
Continuous Improvement Programs
McDonald’s invests heavily in training and development programs for its logistics and supply chain staff. These programs focus on best practices, technological advancements, and process improvements.
By fostering a culture of continuous improvement, McDonald’s ensures that its logistics operations remain efficient and effective.
Collaboration and Communication
Effective collaboration and communication are essential for maintaining a smooth logistics operation.
McDonald’s encourages open communication between suppliers, distribution centers, and restaurants.
Regular meetings, performance reviews, and feedback sessions help identify areas for improvement and ensure that all stakeholders are aligned with the company’s logistics goals.
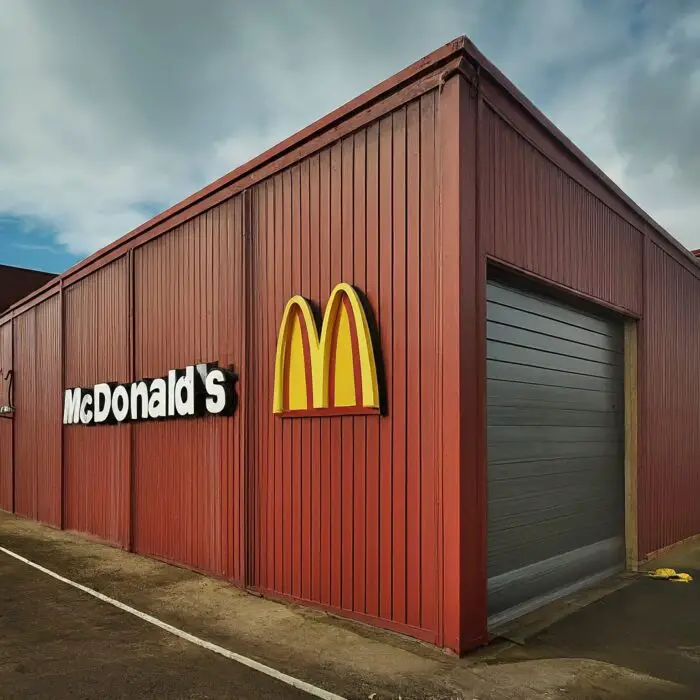
A logistics warehouse.
Q&A
Q: How does McDonald’s ensure the quality of its products globally? A: McDonald’s ensures product quality through long-term partnerships with reliable suppliers who meet stringent quality standards. The company also employs a local sourcing strategy to ensure freshness and minimize disruptions.
Q: What technologies does McDonald’s use to optimize its logistics operations? A: McDonald’s uses advanced warehousing technologies, real-time data analytics, and digital order management systems to optimize its logistics operations. These technologies enhance efficiency, accuracy, and responsiveness.
Q: How does McDonald’s incorporate sustainability into its logistics? A: McDonald’s incorporates sustainability into its logistics by optimizing delivery routes, using energy-efficient transportation, sourcing packaging materials responsibly, and implementing comprehensive waste reduction programs.
Q: How does McDonald’s handle logistics disruptions? A: McDonald’s handles logistics disruptions through robust contingency plans, alternative sourcing strategies, backup suppliers, flexible distribution routes, and rapid response teams that manage and mitigate the impact of crises.
Q: What role does training and development play in McDonald’s logistics? A: Training and development are crucial for McDonald’s logistics. The company invests in continuous improvement programs for its logistics staff, ensuring they stay updated with best practices and technological advancements, and fostering effective collaboration and communication among all stakeholders.
Conclusion
McDonald’s has mastered the art of logistics, maintaining an organized and intact system that supports its vast global operations.
Through strategic supplier partnerships, efficient distribution centers, technology integration, sustainability initiatives, robust crisis management, and continuous training, McDonald’s ensures the seamless delivery of its products and services.
This comprehensive approach not only supports McDonald’s current success but also positions the company for future growth and resilience in an ever-evolving global market.